Дверь от Феррари, капот от Ламборгини: как собирают Fiat Ducato на заводе Sevel - «Fiat»
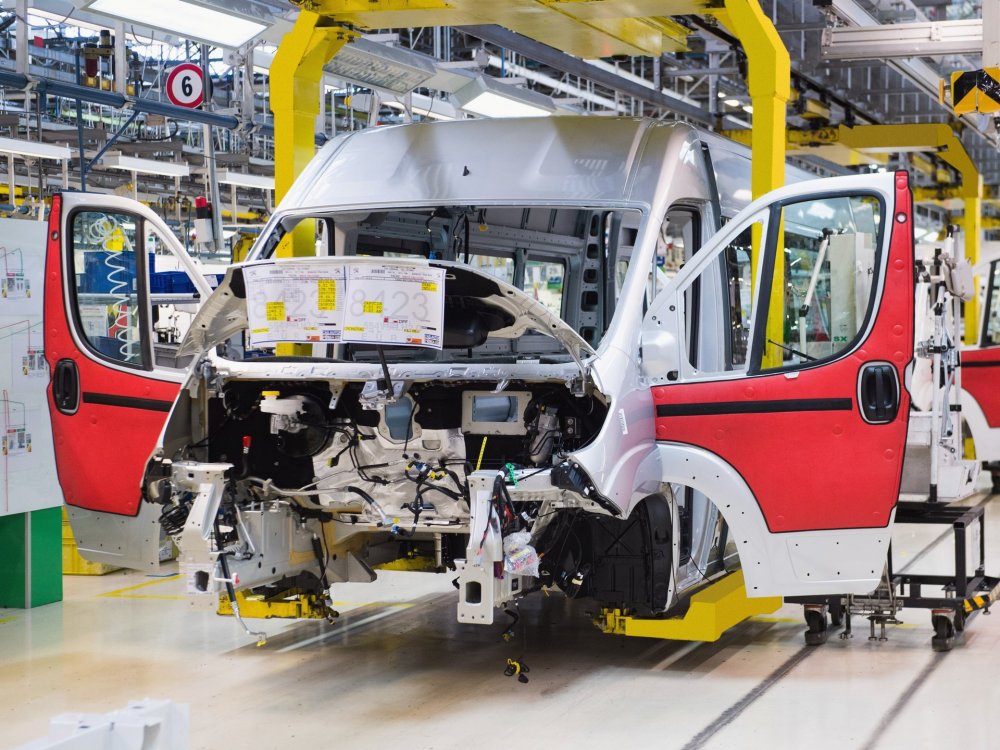
Колеса.ру побывали на заводе SEVEL в итальянской Атессе – крупнейшем в стране и на континенте автосборочном предприятии коммерческого транспорта, где производят Fiat Ducato, составляющий почти четверть всего парка малого коммерческого транспорта Европы. Давайте же вместе посмотрим, как собирают самый популярный малотоннажник!
Завод SEVEL в итальянской провинции близ города Атесса не создает впечатление промышленного гиганта в традиционном понимании многих. Невысокие, выглядящие одноэтажными неброские корпусы, нигде не вздымаются в небо монструозные башни и колонны, не дымят трубы и не грохочет железо, не видно работяг в замасленных спецовках и с суровыми закопченными лицами…. Лишь птицы чирикают в полной тишине на растущих среди газонных полей пальмах…
Однако первое впечатление обманчиво. «Прижатый к земле» SEVEL занимает площадь 1 211 345 квадратных метров, что в переводе на привычные нам гектары – около 120 га. Трудятся на SEVEL 6 300 человек, каждый день на завод приходят 500 фур и 1 железнодорожный состав с запчастями, а готовую продукцию опять-таки ежедневно вывозят 250 автовозов и 8 железнодорожных составов. День за днем ворота завода покидают 1 160 готовых машин!
О тонкостях сварки
Нынешнее поколение Ducato называется X2/90 и выпускается с 2014 года.
Наверное, главная гордость любого автозавода сегодня – это автоматизация производства. На SEVEL она на высочайшем уровне. Робот берет из стопки заготовок полкабины или детали рамы (если машина планируется под борт или будку) и устанавливает деталь на конвейер – это первая операция. Следующий робот подводит к основе боковинки внутренних частей порогов и приваривает их точечной сваркой в десятках точек. Попутно в строго определенных местах с точностью до 0,05 мм привариваются монтажные резьбовые шпильки, проушины, кронштейны, запрессовываются резьбовые втулки. Сотни самых разных автоматов Comau Robotics пост за постом формируют из штампованных заготовок контур будущего Ducato. На каждый кузов в конечном итоге приходится более 7 тысяч точек сварки.
Кстати, надо отметить, что Comau Robotics – это не японские промышленные роботы, как может показаться из названия марки, а итальянские. Comau Robotics – туринская компания, созданная еще в 1973 году и входящая в FCA Group. «Японское» имя на самом деле скрывает итальянскую аббревиатуру «Объединение машин и инструментов» — COnsorzio MAcchine Utensili.
Безусловно, ручные (а вернее, «полуручные») операции есть и на сборке. Некоторые кузовные элементы обваривают роботы, но первоначально позиционируют их люди. Собственно, задача человека – поставить панель на свое место (неточности и ошибки исключены, поскольку в сопрягаемых деталях предусмотрены «ключи», как в фишках «лего») и прихватить несколькими точками сварки ручным сварочным аппаратом, который спускается с потолка на тросиках с моторизованной подвеской строго в заданном месте.
Особая фишка роботов – постоянная самодиагностика сварных электродов. От постоянных разрядов наконечники точечной сварки теряют форму, «растаптываются». Увеличивается площадь «пятачка», а значит, падает сила тока, и соединение рискует стать менее прочным. Поэтому робот Comau после определенного цикла работы подносит наконечники к специальному сканирующему устройству. После осмотра сканер решает, что делать. Если длина позволяет, то робот опускает наконечники в специальный заточной станок, где фреза поправляет их форму до номинала. Если длина приблизилась к допустимому пределу, наконечник заменяется новым.
Статьи / Технологии
Люди и роботы: как делают Skoda Rapid в Калуге
Что лучше умеют делать роботы, а где человеческий глаз и руки незаменимы? Зачем при сборке автомобилей используют клей, а при испытаниях на прочность — обычный крем для рук? Мы отправляемся.
Сейчас у многих благодаря рекламе возникло ощущение, что самые продвинутые автопроизводители одним махом перешли с контактной на лазерную сварку. На самом деле это заблуждение. Да и нельзя рассматривать лазерную сварку как однозначно следующую ступень эволюции в автопроизводстве.
Лазер действительно в некоторой степени легче позиционировать, что повышает точность, но за определенным пределом точности, которым сегодня обладают все роботы контактной сварки, дальнейший рост ее не слишком осмысленен. Можно, конечно, повысить точность с 0,05 мм до «сотки» или даже до тысячной доли миллиметра, но зачем? Габариты автомобиля велики, это же не механизм наручных часов… Такая прецизионность важна в двигателе, но в кузове – хоть Дукато, хоть Феррари — рост точности выше существующих стандартов ни на что не влияет.
Касательно прочности – ровно то же самое. Технология точечной контактной сварки десятки лет назад отработалась до достижения прочности сварной точки выше прочности основного материала. Иными словами, если начать растягивать сваренное соединение, то «пятаки» сварки будут вырываться из листового металла целиком, а само соединение разорвать не удастся. Поэтому лазерная сварка – это не прорыв в плане прочности. Лазерная сварка – это в первую очередь эстетичность, не требующая дальнейшей обработки. Поэтому на сборке Ducato она применяется в основном на поверхностях, которые видны снаружи, и там, где прилегают пластиковые панели. Как правило, это зоны дверей и окон и салон. Для сварки же деталей, находящихся внутри, используется более традиционная точечная контактная сварка. И ещё применяется такой метод соединения, как автоматическая пайка тугоплавким припоем. На примере двери хорошо видны все три вида соединений:
С определенной периодичностью кузовные детали выборочно поступают на автоматический координатно-измерительный стенд, где с высочайшей точностью проверяется геометрия.
А человек всё-таки лучше!
После окраски кузова (на SEVEL красят в 209 различных цветов), автомобили без колес движутся по цеху либо на напольном транспортере, либо на подвесе. Ducato проходит бесчисленное множество постов сборки оборудования салона, тормозной системы и электрики.
Надо отметить, что в сборочном цехе, в отличие от кузовного и окрасочного, гораздо больше ручных операций и, соответственно, возможностей сделать ошибку. Поэтому контроль тут максимальный: рабочий каждого поста ставит штамп на сопроводительные документы автомобиля о проделанной им операции в бумажном и электронном виде.
Кстати, над многими сборочными постами конвейера установлены таблички – «Феррари», «Ламборгини» и так далее. Но имя «Феррари» над постом установки дверей не стоит воспринимать буквально. Это не дверь от Феррари, разумеется. Такие имена просто удобнее для рабочей коммуникации: их проще запомнить, чем цифры и буквенные коды. В соседнем цехе, к примеру, для того же самого используются не менее звучные названия футбольных команд!
Роботизированная тележка, везущая тормозные трубки, движется вслед за устанавливающим их оператором так, что тому не приходится делать даже один лишний шаг назад.
Робот-«грузчик» подносит собранное торпедо. На фотографии виден экземпляр в праворульной версии для заказчика из Великобритании
Ближе к концу производственного цикла машина приходит на пост так называемой «свадьбы». Снизу подъезжают две тележки. На одной лежит двигатель на подрамнике с КПП, передними стойками и рычагами подвески и бензобак, на второй — задний мост с рессорами. Сверху на них опускают кузов. После «свадьбы» автомобиль приобретает законченные очертания и передвигается по конвейеру на своих «ногах», зацепленный за ленту транспортера одним колесом.
Итог всех усилий закономерен: лидирующие позиции Fiat Ducato в сфере легких грузовиков…
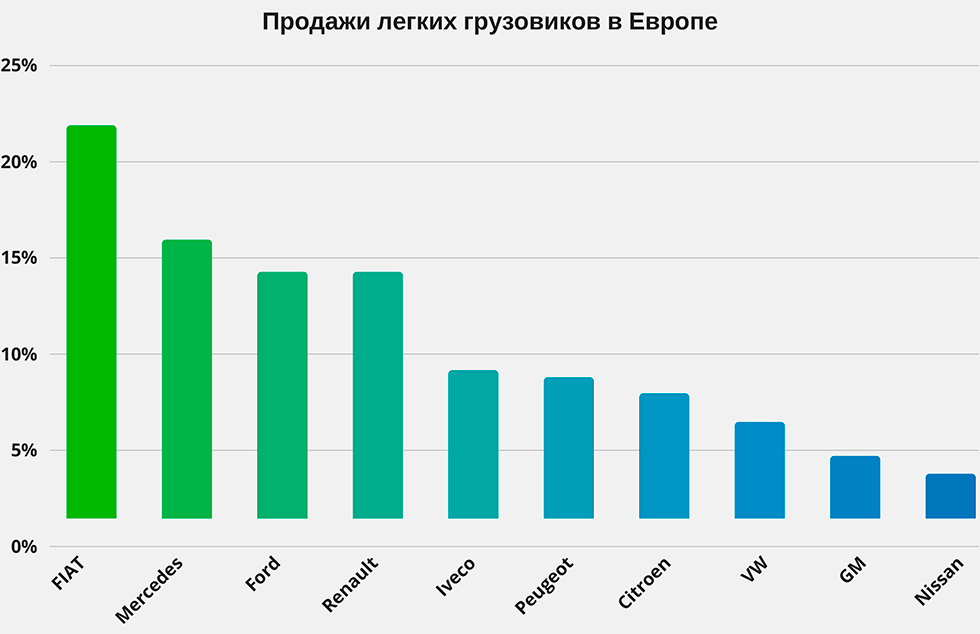
А вы знали?
Ну и напоследок – несколько любопытных фактов о работе завода SEVEL.
- Высочайший уровень техники безопасности – строго запрещенная (иначе – штраф) к снятию в течение рабочего дня спецодежда (ботинки с металлическими вставками в носах, очки, спецовки – у всех), разнообразные и многоэтапные барьеры вокруг опасных и просто подвижных механизмов, безупречное освещение повсюду, многочисленные плакаты, где в юмористической форме демонстрируются возможные ошибки, приводящие к травмам. Платить работнику компенсацию за травму на производстве и спешно менять рабочий график из-за внезапно выбывшего сотрудника гораздо дороже, чем предотвратить все это.
- Если на каком-то посту обнаружена пропущенная на предыдущем операция, через радиотрансляцию цеха включается сигнал. Но не тревожная сирена, а… музыка. Обычно что-то из современной попсы: Luis Fonsi, Katy Perry, Sigala и т.п. Также номер поста высвечивается на всех центральных мониторах в проходах цеха, и к нему спешит тим-лидер, специалист-универсал, который устраняет недоработку члена своей бригады, не отрывая его от работы и не останавливая конвейер.
- В сборочных цехах то и дело встречаются небольшие фуд-зоны, где стоят автоматы с легкими закусками и напитками, установлены стулья и столики. Там рабочие могут перекусить в течение дня.
- Средний возраст работников SEVEL – 46,3 года, средний стаж работы на предприятии – 18,8 лет, доля сотрудников-женщин – 21,3%.
- Профилактический простой завода в году – всего одна неделя. На неделю в середине августа обычно SEVEL закрывается на корпоративный отпуск.
- Конвейеров для разных моделей нет. По общей линии непрерывно идут разные модели: высокий фургон, низкий, удлиненный, бортовой грузовик, голое шасси и так далее.
- Второй этаж в кузовном цеху завода – для роботизированной подачи и перемещения запчастей и целых кузовов, люди там не работают. На втором этаже цеха – 16 километров транспортных линий.
- В бак выходящего с конвейера автомобиля заливают всего 2,5 литра топлива.
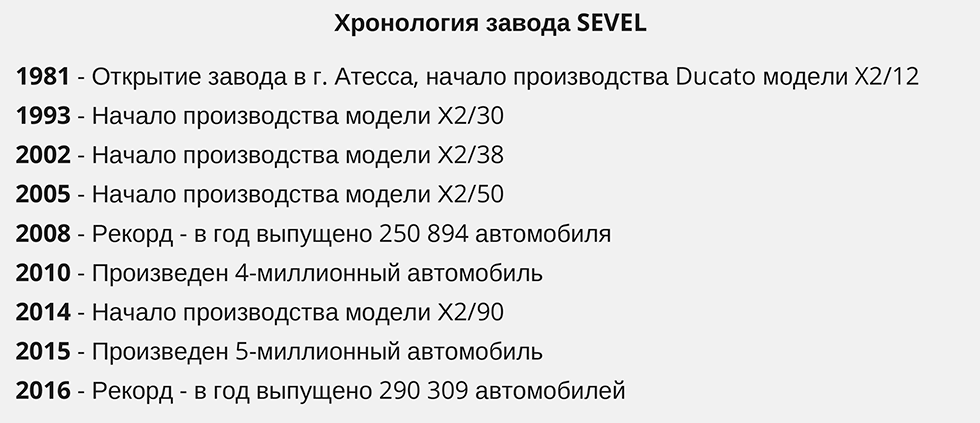